The logistics sector is rapidly evolving with new innovations promising to streamline operations and enhance efficiency. However, these advancements come with significant challenges and barriers, including high costs and technology that becomes obsolete quickly. In this blog, we explore the current state of automation in third-party logistics (3PLs), highlighting practical insights and real-world examples of innovation and the hurdles that need to be overcome
In a nutshell…
- Robotics and automation can enhance logistics, but are costly and may quickly become outdated.
- Channel management and product variety complicate automation.
- Collaborative solutions are key, integrating existing technologies rather than relying on end-to-end systems.
- Flexibility and scalability are crucial for high-growth brands.
- Understanding and solving specific logistical problems is vital before investing in automation.
A closer look…
Automation in action
Innovative solutions in 3PLs are transforming logistics. Retail Hive members are exploring how robotics can streamline operations, everything from basic mechanisation to advanced AI. However, affordability and ROI both remain significant hurdles to getting solutions rolled out. One approach that has proven popular is composable automation, starting with a base system and gradually adding capabilities to allow for quicker updates and adaptability to new technologies.
A problem many members face is managing multiple channels (i.e. store, concession, eCommerce) within a single warehouse. Integrating automation for different product sizes and handling both small online orders and large wholesale shipments requires flexible and adaptable solutions. Innovations like pocket sortation and collaborative robots can help manage these complexities, improving efficiency and reducing manual labour.
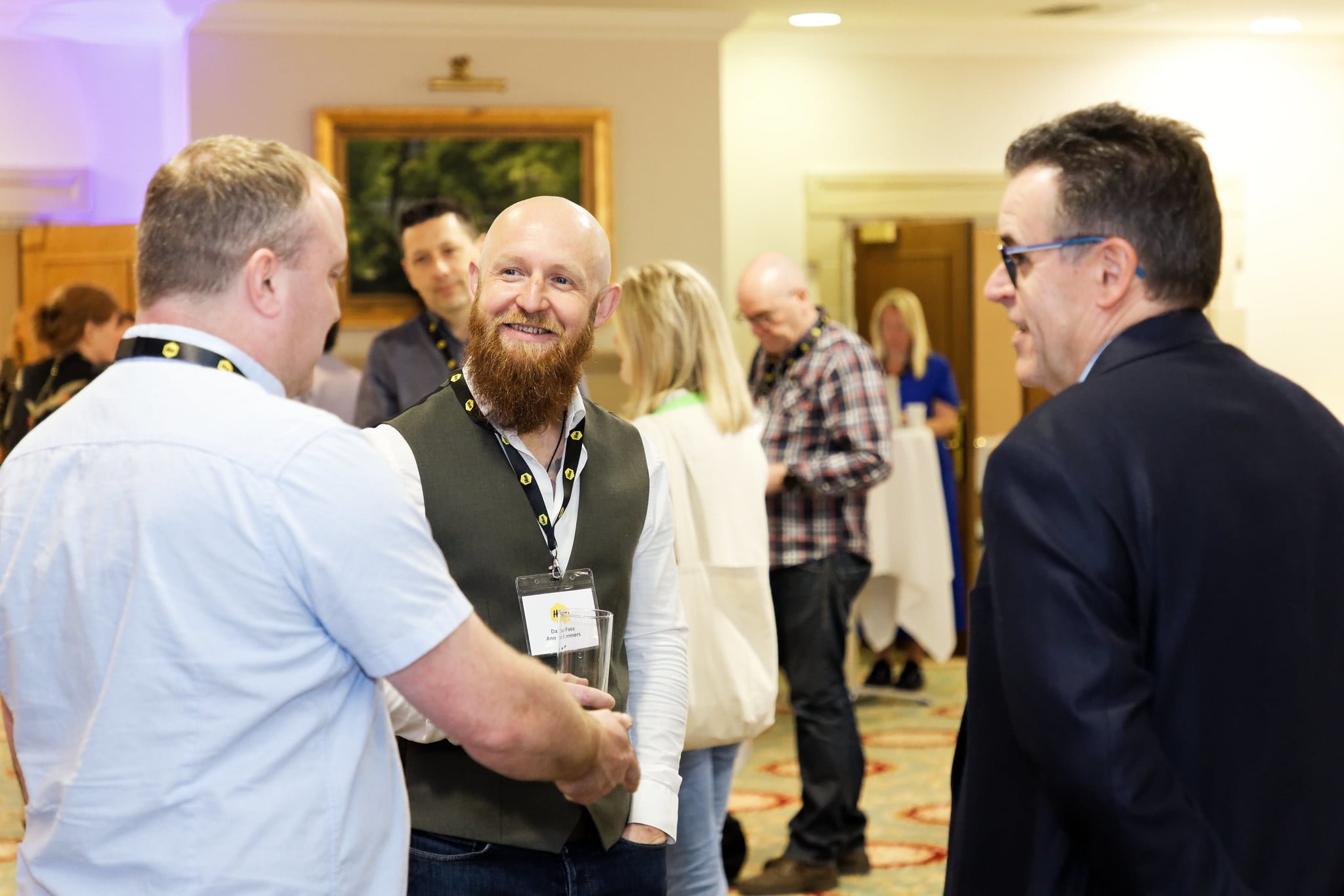
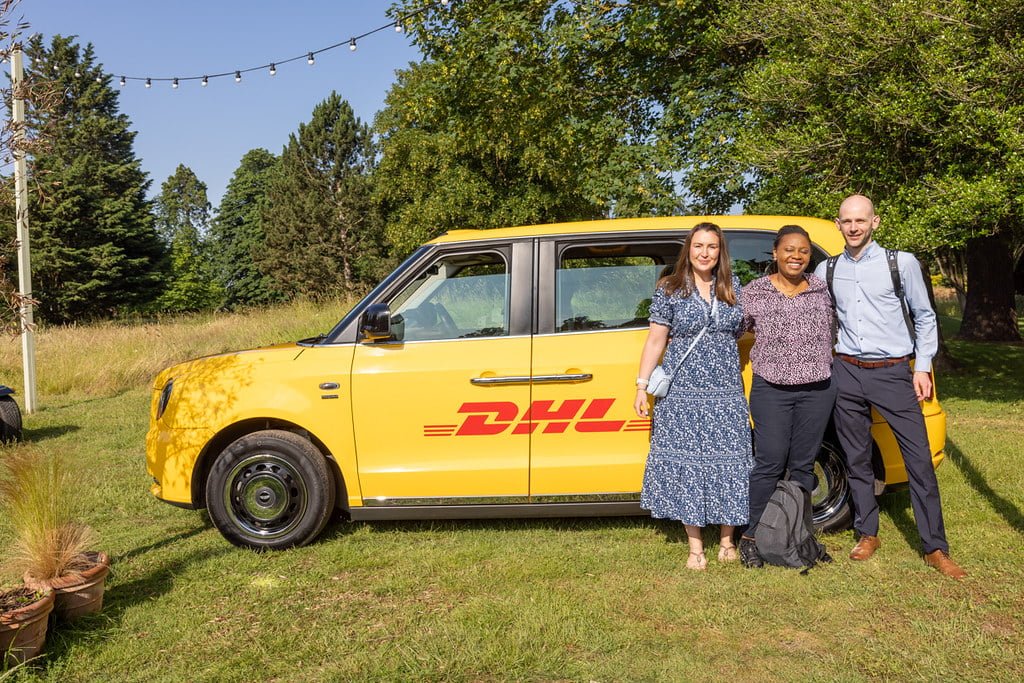
It’s important not to overlook the importance of collaboration between 3PLs and brands. By leveraging 3PLs’ expertise and existing infrastructure, brands can focus on growth while the logistics partners handle fulfilment. For instance, automated tote-to-person systems in 3PL warehouses allow for rapid scaling without the brand having to make substantial upfront investments.
Still to do…
Despite these advancements, several barriers need to be addressed. High capital investment and the rapid obsolescence of technology are major concerns. We’re also hearing that retrofitting legacy warehouses for automation involves significant structural changes, such as ensuring smooth, uninterrupted surfaces for robots to operate efficiently, which isn’t always easy to do.
One point on which most members agree is that it’s really important to understand the specific logistical problems that AI can address before investing in automation. For example, not all solutions are suitable for every product category or order volume. Testing modular and flexible solutions can help identify the most effective technologies for particular needs without committing to large-scale investments prematurely.
There are plenty of new opportunities, though, such as robotic arms for container loading/unloading and automated sorting systems, which can further enhance efficiency. Collaboration with suppliers and continuous improvement initiatives, like RFID scan taggers, can also drive innovation and sustainability in logistics operations.